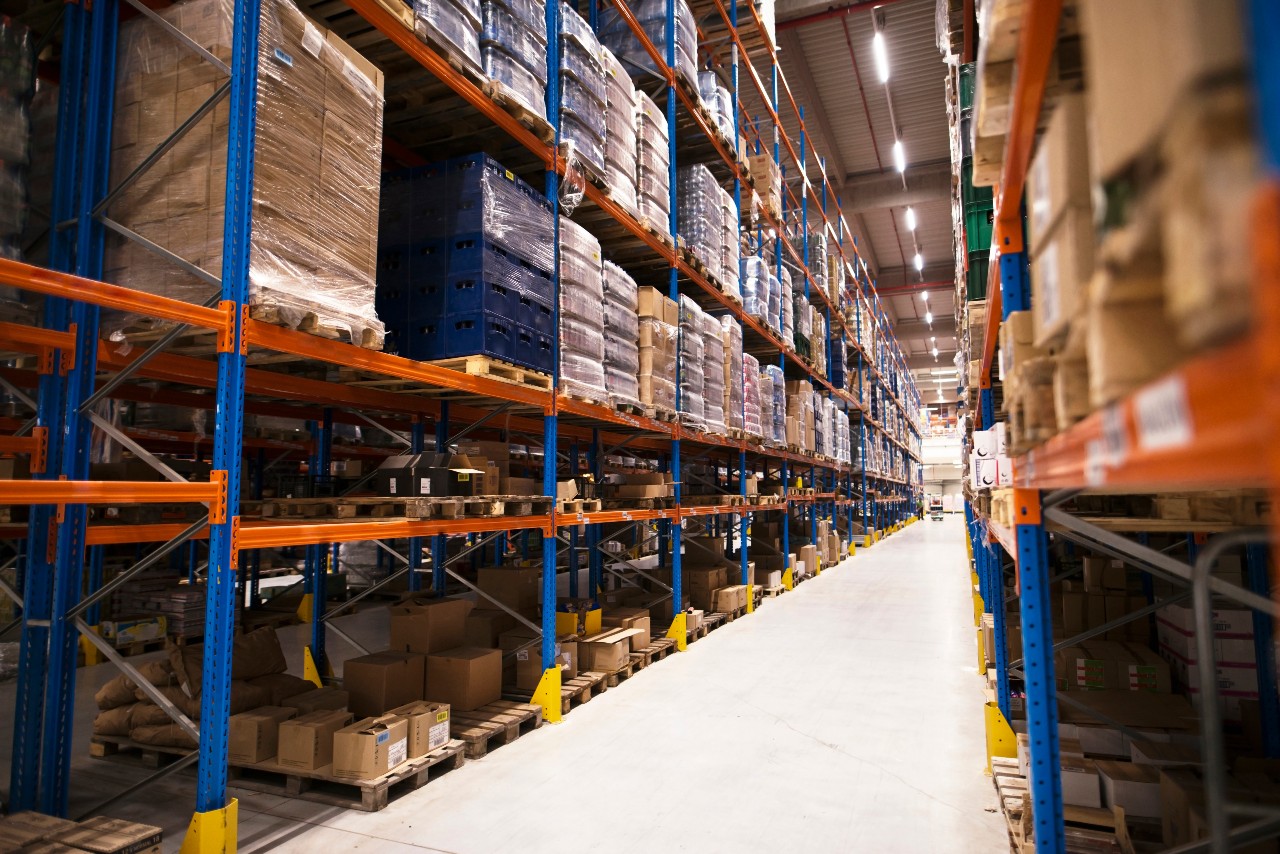
Dopo aver parlato dell’importanza del picking nella logistica di magazzino, è arrivato il momento di occuparci delle diverse tecniche con cui è possibile applicarlo, mettendolo in relazione con le capacità di svolgere tale attività da parte di un sistema WMS.
Perché esistono diversi sistemi di picking?
Come anticipato, abbiamo già affrontato la centralità del picking nell’attività di magazzino in un precedente articolo ma, prima di parlare delle differenti tipologie di prelievo, è opportuno soffermarsi brevemente sulla natura di questa operazione.
In senso stretto, il picking si occupa della selezione e del prelievo di merci o materiali dagli spazi di magazzino per destinarli alla lavorazione o alla spedizione. Il prelievo è l’attività più complessa in un magazzino, in quanto necessita di una forte componente di manipolazione della merce e, molto spesso, in piccole quantità.
Proprio la sua complessità ha reso necessaria la creazione di diverse metodologie di applicazione, dal più semplice picking manuale, con l’operatore che si muove tra le aree di magazzino, alle tipologie più complesse che prevedono una forte, quando non totale, automazione del processo.
Quando un magazzino supera determinate soglie dimensionali in termini di spazi e volumi oppure in termini di numero di movimentazioni o, ancora, se ci si trova di fronte a certe complessità operative, diventa indispensabile l’implementazione di un sistema WMS in grado di pilotare l’azienda nell’attuazione dei prelievi in differenti modalità. A seconda della tipologia di organizzazione, si andrà quindi ad implementare la modalità di picking in grado di garantire il maggior livello di efficienza possibile, sia in termini di rapidità che di precisione.
I principali sistemi di picking a magazzino
Quando gli articoli presenti negli ordini hanno una consistente ripetitività, è possibile affidarsi al picking massivo, in inglese batch picking, una modalità di prelievo che, proprio attraverso il supporto di un software gestionale per il magazzino, garantisce efficienza operativa, elevata produttività e tempi ciclici ridotti. Ha però lo svantaggio di dover effettuare, a “valle” del prelievo, un’attività di composizione degli ordini chiamata ventilazione.
Se l’operatore effettua giri di prelievo per un insieme limitato di ordini, possiamo parlare di picking raggruppato o multi-ordine. Questa metodologia permette di prelevare gli articoli con il medesimo SKU in un unico passaggio dell’operatore, raggruppandoli automaticamente grazie alla guida del sistema WMS, indispensabile per garantire il corretto governo dell’intero processo.
Una delle modalità di prelievo più diffuse è il picking per ordine, effettuato attraverso l’utilizzo di tecniche come il pick&pack, che consente di effettuare l’attività di handling una sola volta, unendo la fase di prelievo a quella di impacchettamento.
Ottimizzare il picking sfruttando le potenzialità del WMS
L’utilizzo di moderni sistemi gestionali di magazzino come Gulliver di Kube Sistemi presenta innumerevoli vantaggi operativi quando si tratta di ottimizzare il prelievo degli articoli stoccati.
Un esempio è rappresentato dalla capacità di un WMS di indirizzare l’operatore al prelievo in funzione del numero di pezzi da prelevare: il sistema indicherà se effettuare il prelievo di pezzi sfusi, di confezioni o di master carton in base al tipo di confezionamento presente a magazzino ottimizzando i movimenti dell’operatore.
Indispensabile è anche l’apporto di un gestionale di magazzino anche per il mondo e-commerce, quando l’attività di picking si sviluppa su poche quantità per ordine, necessita di grande velocità e precisione, e si adatta ad essere sviluppata con metodologie “lean” come il pick&pack.
Non solo software: apparecchiature a supporto del picking
Un magazzino che lavora principalmente con attività di picking necessita di tecnologie hardware a supporto dell’operatore. Spesso in queste realtà è necessario dotare il personale di strumenti che permettano di lavorare con le mani libere.
Se nella gestione del magazzino vengono già utilizzati in modo consistente i codici a barre sui prodotti, può essere opportuno valutare la dotazione di terminali indossabili per gli operatori, in modo tale che possano interagire con il sistema WMS tramite un display ed effettuare l’attività di handling senza dover appoggiare ogni volta il proprio terminale.
In altre situazioni è invece consigliabile l’implementazione di apparecchiature a tecnologia vocale, oggi abbastanza diffuse nei centri logistici della grande distribuzione o negli ambienti dove può risultare difficoltoso l’utilizzo di terminali mobili.
Soluzioni abbastanza diffuse nei magazzini e che generalmente possono incrementare, se ben implementati, la produttività del picking, sono i magazzini verticali e i sistemi di pick/put to light, in quanto aiutano, gli operatori nell’attività di prelievo e di composizione dell’ordine finale, anche visivamente.
Gulliver, il WMS di Kube Sistemi, supporta queste ed altre metodologie, oltre alle tecnologie necessarie in una logistica moderna ed efficiente, forte dell’esperienza maturata in oltre 25 anni di presenza sul mercato e del gran numero di progetti realizzati con successo.